Iron-In-Spring-Valley-Wisconsin
Created: February 7, 2021
Last Revised: October 20, 2023
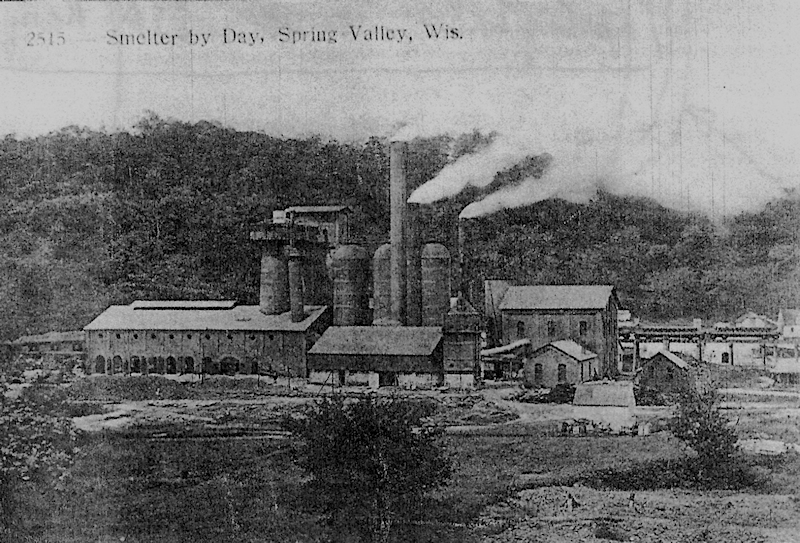
Smelter in Operation, before 1912
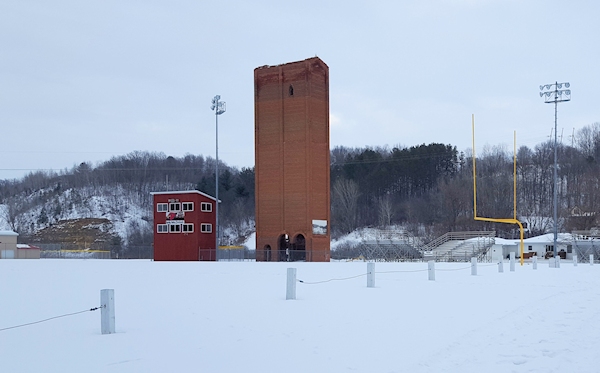
The Elevator is all that Remains, February, 2021
French Creek Valley Home
Back to Blacksmithing
Back to My Shop
Contact Us
Here's How I Learned about the Smelter
Back in the late 1980's I had just gotten into blacksmithing and one of the professional smiths in our club suggested that we make our own anvils,
all the way from
mining and smelting ore to forging and finishing them. Well, that project never did happen, but it spawned several other related activities over many years.
However, we actually did participate heavily in two smelts on The U of M grounds between 1991 and about 1995, that produced forgeable "Wrought Iron".
My wife and kids and I had recently moved from St. Paul Minnesota out into the country about 6 miles northwest of Spring Valley, Wisconsin.
Talking with local folks, we had learned that, back in the late 1800's and early 1900's there had been a smelter producing "pig" iron on the north side
of Spring Valley, Wisconsin.
Also, folks mined iron ore quite close to town during that period.
So, when I met Ted Vanasse during those late '80's, I told him that our gruop would like to mine our own ore and then convert it to forgable iron and steel.
He graciously produced for me the following history of Spring Valley's mining and smelting adventure.
Iron in Spring Valley
by Ted Vanasse
Some Iron Making Background
The obvious requirement in making iron is the ore. Ore, of course is found in varying quantities throughout the world.
Countries with the highest production are, first of all, the United States, and then Russia,
France and decreasing amounts in other countries. The following shows where and how much ore is produced in the United States:
Minnesota = 68 Million Tons
Michigan = 13.5 Million Tons
Alabama = 6 Million Tons
Wisconsin = 2 Million Tons
The kinds of ore of which there are several, is of prime importance in the production of iron.
The most important ore in the US is HEMATITE.
This ore or substance, is familiar to everyone as red iron oxide, or rust.
Many rocks and other minerals are colored red by hematite, such as red Jasper, red agates, etc..
85% of all ore produced in the US is hematite, usually from the north.
A second ore, that used in the Spring Valley (Wisconsin) smelter, is Limonite, also called brown hematite. This ore is 1% of US production.
A black often shiny ore is MAGNETITE, or lodestone. It affects compass needles and is itself a magnet capable of picking up bits of iron.
Ten percent of this ore is found in the US although Sweden has long been famous for its fine steels made from this ore.
SIDERITE is a gray brown ore of poor quality and is seldom mined.
The final ore, which has acquired considerable importance in northern Minnesota is TACONITE.
This is usually hematite or other ores occurring as specks and streaks in other often very hard rocks.
Great roller mills mash and pulverize the rock to produce taconite pellets for use in steel mills.
Before explaining the structure of the Spring Valley Smelter, which incidentally was quite an
old-fashioned and comparatively simple affair, it should be mentioned that making iron was much
like making a cake. The best results came if the recipe was followed.
Thus every substance or ingredient that went into the production of iron was weighed carefully and amounts were added only after complete chemical analysis.
The usual substances were Iron Ore, coke or charcoal to burn and produce the high heat,
limestone to collect impurities in the form of slag and an enormous amount of hot air
blown in to increase the rate of burning and produce the necessary heat.
The recipe then, after all conditions were considered, consisted of:
1 3/4 Tons of ore
3/4 Tons of coke
1/4 Tons of Limestone
4 Tons of air
This of course, does not include the thousands of gallons of water
necessary to cool the outer portions of the furnace.
The three great ovens in the Spring Valley structure are often misunderstood and misinterpreted.
All three were completely filled with loosely spaced fire brick into which cold air was blown to be heated to perhaps 500 degrees.
The heat was introduced into the bottom of the ovens and consisted of gas produced by the furnace itself and piped through
underground passages or tunnels to the curved entrances.
Each oven when thoroughly heated receives the cold air.
When hot it was blown into the base of the furnace through about a 3 foot pipe from which tuyeres projected at intervals
into the lower part of the burning coke. Immense pumps in the engine room furnished the blast for this process and others.
For example, the engine room also contained pumps to draw water from the river to fill the huge water tank, which stood almost as tall as the ovens.
About the Smelter
The rest of this story will be based on the accompanying lettered photographs. Some of which were furnished by Everett Brown.
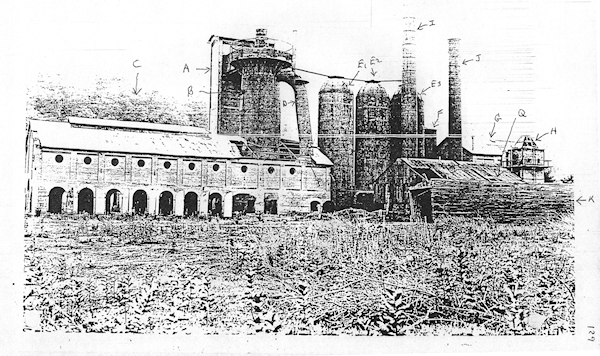
Photo #1, The site some time after operations ceased
The elevator tower (A) still stands at the corner of the football field, and is all that remains of the furnace.
Two doors gave access to the tower at the bottom: A large wide door at the lower southwest gave space to wheel wagons of ore, coke,
and limestone onto the elevator platform. This platform and its load were hoisted to the upper level of the smelter by cables run
by a drum and engine or motor at the lower left. A single narrow door led to this area, which was also the foot of the stairs which rose,
flight by flight along the tower's north wall.
The village fathers decided that the stairs and also the upper reaches of the furnace were dangerous; so two bottom flights were removed.
As youngsters we circumvented this by leaning a board up to the third flight and climbing it.
More often to reach the top, we simply climbed the ladder on the large stack.
This brought us to the top of the third stove.
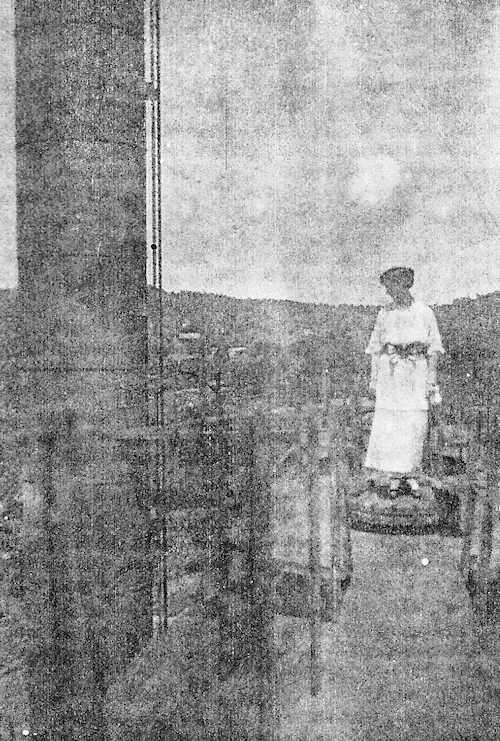
Woman Standing On Top of Large Stack 1, (E3)
An iron walkway with cable guard rails led from there to the top of the smelter.
This walk is shown running from stove to stove to the smelter platform.
B. The furnace and its operation are sufficiently shown in this sketch (sheet 7, below).
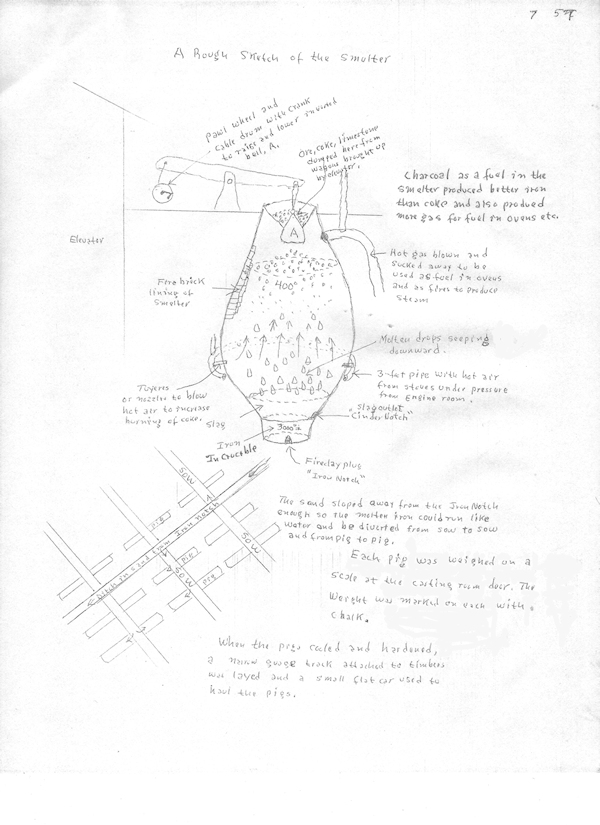
Sheet 7, The Blast Furnace Explained
The chemical reactions involved are not included. Water flowed continuously through pipes around the crucible because of the great heat.
C. The casting room, which during casting, must have been hell, itself.
The water thin iron with its intense glare are shown on several photos taken at night. This too is explained in part on sketch 7.
D. This large pipe emerging from the space above the melting mixture in
the smelter, is probably one of the more important parts of the total structure.
It carries gas, either by sucking it or by blowing from below, to be used as fuel in the three stacks
and for fire to produce steam below "H" for the engines.
E. The curved pipes H, at the bases of the stoves, are entrances to carry gas from D as fuel to heat the air
to be blown into the lower part of the furnace.
It reaches the pipes H through a tunnel under the heavy Iron covers, N. As boys we crawled in these tunnels but certainly didn't
become any cleaner because of the abundant fly ash.
This fuel was burned in the stove until the brick interior became hot;
then a blast of cold air was introduced to be heated while a second stove was used for hot air for the furnace.
Thus one after the other stove was used in succession. The interiors of the stoves were completely filled with fire brick,
stacked with spaces between for circulation of the burning gas filling the structure.
The temperature of the stoves was checked frequently by rolling back the curved pipe, which had small wheels flanged to a short track.
A copper bushing-like object was inserted on an iron rod, heated and then dipped into a container of oil.
By that process the stove temperature was determined.
Other pipes carried the gas to two or three furnaces under the structure H. Steam produced there was sent to the engines in the engine room, G.
Photo in sheet 4 shows the great engine with the large cylinder in the darkness above.
Other smaller engines used steam for other purposes. The engine was simply a large Corliss air pump.
F. The water tank is probably at least twelve feet in diameter and forty feet high. With those dimensions it would need about 14000 gallons.
A pump in the engine room kept it full by use of an underground 8 inch pipe that ran east to the river.
Projecting from the riverbank, a boxed-in area with a coarse screen in the river end, held the iron pipe with an elbow to hold it in the water.
Trouble occurred often by grass and leaves plugging the screen.
G. The Engine Room:
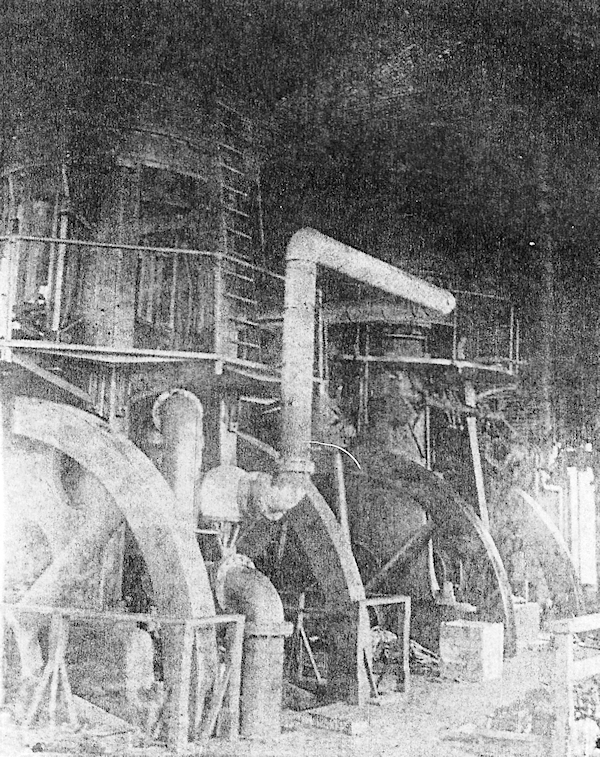
Engine Room
The huge wheels were from 10 to 14 feet in diameter.
When the air blast was stopped during a time of casting iron, a large pole, about like a wagon tongue, was used to pry on a spoke
to start the engine in motion again. The second engine was not operable at the time of the photo as may be seen by the unconnected steam pipes.
H. The smallest of the three chimneys had fallen before this photo was taken, Below, in the square furnace room,
gas fires below a huge boiler produced steam for all uses. More than one fireplace door made the structure
look like the stoke hold on a coal-burning steam ship.
Fly ash was thick everywhere and by only a miracle climbing boys did not fall into the space behind the boiler.
A wrapped pipe carried steam to the engine room.
I. The tallest and largest stack. During one renovation, when new stoves were built,
fifty feet was added to the top of this stack. J was a smaller stack, but served the same purpose as the large one.
It created a draft to pull the flue gas along and also carried away the smoke.
K. This was a long shed to hold three or four cars, probably to keep charcoal dry temporarily.
It was of later construction. Snow or water in the ore or limestone made little difference in the smelter.
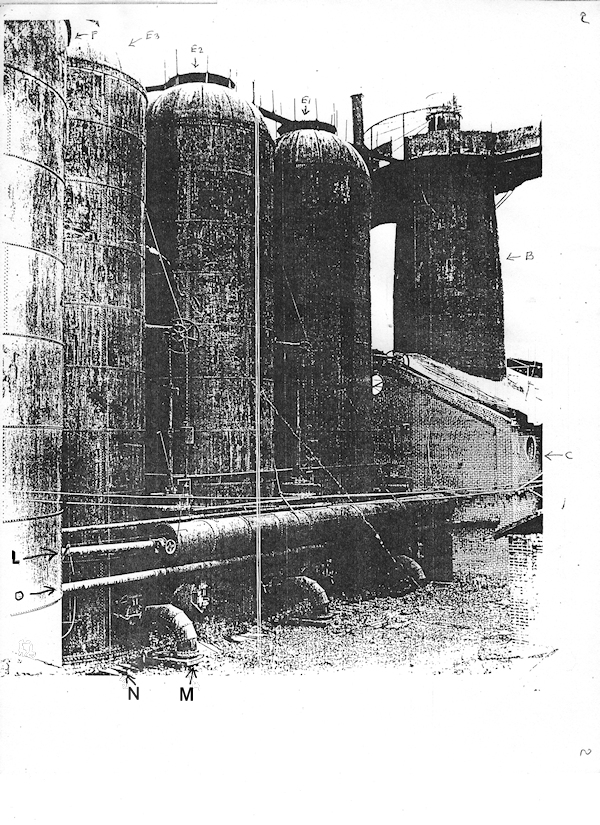
Sheet 2, The Preheating Stoves
L. In Sheet 2, this is the air pipe from the engine room.
It enters the large pipe, which was required when hot air from one of the stoves was drawn out for the furnace fire.
M and N are explained along with E, the stoves were also called ovens.
O. A water pipe running to the casting room to cool the crucible and to the area where slag had to be cooled.
(When I accompanied my brother to the engine room with my father's dinner bucket, a workman turned the cold water hoses on
the hot slag so I could walk across with my bare feet.)
Q. The machine shop.
Machines not in the engine room were here. One was a steam engine-driven dynamo that produced electricity for lights and a few motors.
Somewhere in this area (reference "P" is missing) was a dust collecting chamber to aid in making clean, hot fires farther along.
R. In the photo on page 3 three cars of ore stand on the elevated track.
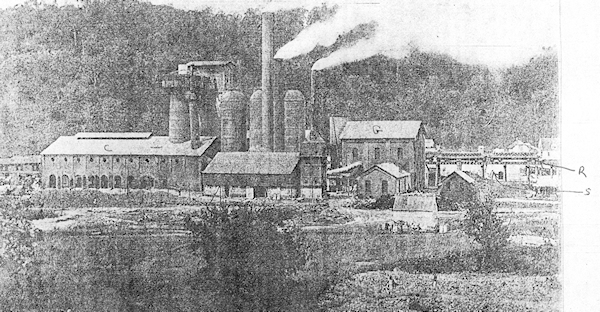
Ore was dumped near the end, limestone and coke near to the elevator. When the furnace shut down finally there was still a pile of ore remaining.
S. Arnold Lewiston, who lived in one of the row of houses west of the furnace,
says that there were eighteen charcoal kilns in the two rows to the west of the rail road tracks.
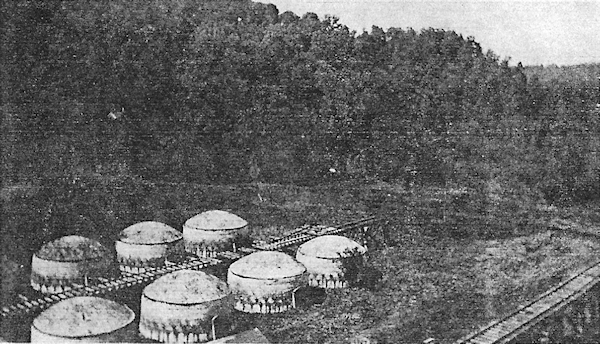
S. Charcoal Kilns with Railroad Tracks
A track also ran between the rows. They must have used a lot of wood, if charcoal iron was made very often,
but I never heard of any farmer selling wood to the furnace. Near Madson's saw mill, and also south and a mile west of Wildwood,
at a place that we called the slag pile, but is now Boston on maps, there were also rows of kilns.
A few people mistakenly call them brick kilns. However, they too produced charcoal. Bricks are not made in such structures.
As may be seen in any photo of Lowater's brickyard, or at the Menomonie Brick Company site.
The information and photos shown here tell only a part of the smelter story.
Many details have been left out, partly because of lack of information, and partly to avoid many of the minor details.
A few of those details could include the rest house where the casting room workers ate their meals and rested briefly.
Also the thick wooden shoe soles that lay scattered about, and which no one had the foresight to pick up a pair.
The piles of pig iron that Jous Rogstad loaded into cars, the chemical laboratory, in which one of the Footes analyzed everything until
he trained Andrew Lewiston to be the chemist, the rust-weakened rings in the stack ladders that we climbed, the iron we salvaged from
the slag piles and sold to Kamke for our 4th of July money - these things and many more could more nearly complete the story.
As a final note why not look up Iron in the World Book or any good encyclopedia. Much of what I have written is there.
.
Here are some additional pictures that show various details:
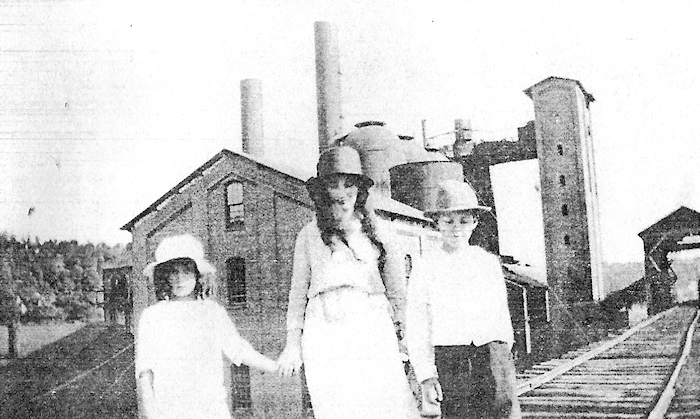
A good view of the backside of the "Works" showing most of the Elevator, and with children in the foreground
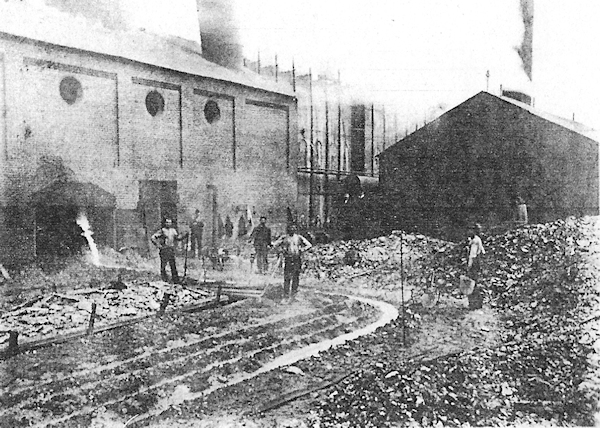
The Cinder Notch Open and Slag Running
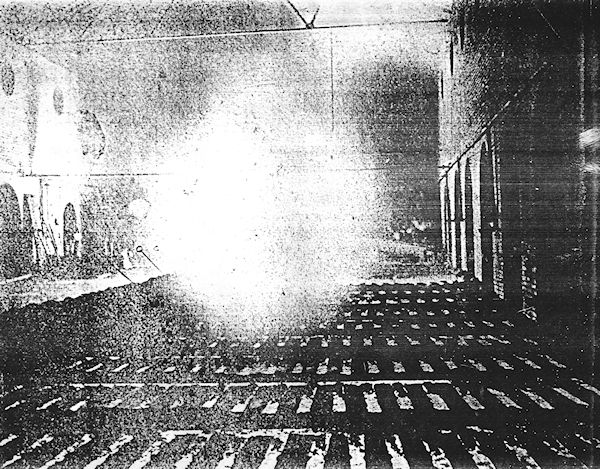
The "Pouring" or "Casting" Floor. The glow of the white hot cast iron coming out of the furnace
overpowers the camera in the center of the image.
The rows of rectangular shapes in the foreground are the freshly poured "pigs" of iron.
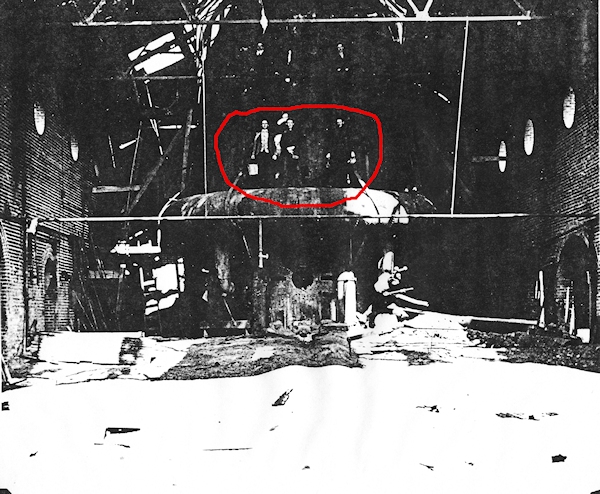
The furnace and building in poor shape, many years after shut down.
You can barely see 3 men standing on the tuyere ring for scale.