1000 Watt ZVS Induction Heater Notes
Created: November 24, 2016
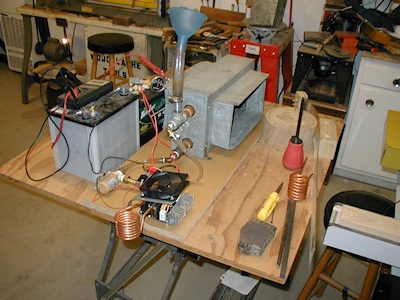
My Third 1000 Watt ZVS Induction Heater Setup
Just before I destroyed it
French Creek Valley Home
Back to Blacksmithing
Contact Us
This is a page in progress!!
Here are the main points that I want to cover:
1. The glowing steel that you see in the coil on the youtube videos is NEVER as hot as it looks.
2. Somebody needs to unravel the "Chinglish" instructions that I find on a couple of the websites that sell them.
3. You can't really heat steel well enough to do any real forging because of the reduction of internal "friction" to the varying magnetic
field in ferrous metals
as the steel reaches its transformation temperature (which in the range of about 1450 to about 1550 degrees fahrenheit, for plain carbon steel).
The steel just doesn't get much hotter than that.
4. So, why doesn't the steel get hot enough? That's because the frequency of the circuits that are sold as "1000 Watt ZVS Induction Heaters"
with about 9 mfd of capacitance have a tank circuit oscillation frequency of about 100 K Hertz. I think you need to be down in the 30 K Hertz range
to get steel parts hotter.
5.Why it breaks, What breaks, and How to Fix It
1. The Glowing Color
I ain't no expert, but it appears to me that the CCD arrays (the camera's picture sensors) aren't color balanced with hot steel in mind. I have taken
many pictures and have produced many amatuer videos of "hot iron" and the iron ALWAYS glows brighter in the picture than it does in reality.
If you watch a few videos of these induction heaters (the 1000 Watt, $30+ dollar kind) you can often see that steel in the coil glowing so brightly that
it looks to be a high yellow color (about 2000 degrees F) or even white (about 2300 to 2500 degrees F). In actuality, a piece of steel that hot would
be sparking vigorously as it prepares to melt.
The highest actual COLOR that I have seen using 3 different examples of this heater is what I'd call a "medium red" (about 1400 degrees F).
Have you seen a couple of videos where the guy takes the temperature of the steel? Have you ever seen a reading much over 800 degrees C (or about 1500 degrees F)?
2. Chinglish Instructions
I don't mean to sound derogatory by using this term, but it IS fitting since it deals with the language and cultural differences between the English language and
the Chinese language. Maybe, when the Chinese technical writers tranlate into other languages, these problems don't exist, but they sure create problems here,
for me.
Here's my ongoing attempt to do some unravelling:
Unravelling ZVS 1000 Watt Heater Chinglish
There may be some duplication of this page within that document, but I hope you will find most of it useful.
If you see anything here or there that doesn't make sense to you, or if you see something that you feel is downright wrong, please let me know.
3. Steel's temperature stops increasing
It's the resistance to the magnetic oscilltions that causes molecules to rub against eachother and thereby heat up the part.
Again, when the steel gets hot enough to undergo physical changes at it's trandformation temperature, the material's structure changes to one that
doesn't resist the magnetic fields as much, so the part reaches an equilibrium temperature and pretty much stays there.
4. Frequency Too High
Commercial units run at frequecies well below the 100 K Hertz that this one does. I don't know why no one else has already commented on this issue.
One expirement that I plan to run is to use the capacitors and inductors from one of my failed boards in parallel with a working unit.
I think this will reduce the frequency by a factor of two.>br>
If it does work that way, I should be able to get my steel to a much higher temperature.
if THAT works, then I'll try adding a third set of L and C components.
Another frequency-related point the no one has mentioned yet:
Copper doens't seem to heat up at all with this unit as it is. Yet the general info on the subject seems to imply that "anything that conducts electricity"
can be induction heated.
I have just received my first graphite crucible. I assume that its characteristics are more condusive to inductio heating with this device than some non-ferrous
metals.
I think we all have seen solder and aluminum (sorta) being melted in those graphite crucibles. At this point, it's my assumption the the induction heater
heats the crucible wall and that heat is conducted to the metal within.
We will see.
5.1. What breaks, why and how to fix it
Before I even get started here, I strongly suggest that you don't even start to play with this thing unless you have a fairly accurate 0 to 30 amp meter
in series with the power supply and a good volt meter across the input.
If the power supply/battery is so small that the input voltage drops below about 11 volts, you may cause the unit to fail to oscillate, which may or not destroy
it.
My proof of expertise:
So far I have smoked or otherwise caused 3 of these things to fail.
For the first two units, I had just run them "out of the box", hooking them up to a 12 volt battery. Note that I had used a small garden tiller battery
at first.
I still don't know what I did to the first one. It had worked for several days, then one day it just didn't work anymore.
The little green LED still lit, but it drew no current at all.
The second one failed when I shorted a couple of turns of the work coil with the piece of steel that I was heating.
But, by that time, I had added a little 12 volt water pump and a pretty good sized
heat exchanger to the work coil. And I added a 12 volt 3 inch muffin fan to cool the circuit board.
In addition, the system is currently powered by 2 12 volt car batteries, for a total of 24 volts to the circuit.
A pretty good size arc and "snap" occurred and the ciruit just quit ocsillating (quit working).
After that experience, I did some more googling and noticed that one guy had slipped some high temperature fiberglass sleeving over the while work coil.
I immediately ordered a one meter piece of the 6.68 mm diamter stuff, which was just barely enough to cover the whole work coil.
I got mine on EBay:
1meter- Manhattan F240-2AWG (6.68mm) 240 degrees C Fiberglass high temperature sleeving
It took a long time to get here from Taiwan, so I went to a local electric motor shop to get some. They had a similar sleeving that was just over
1/4" ID. I got some of that, too. It took several minutes to thread it over the work coil, but it worked, too.
The third one failed because I attempted to heat a piece of half inch water pipe.
By now, I had added the fiberglass sleeving to the work coil.
With this setup, I tested the heating affects on several small test pieces of steel, while observing the current. In most cases, the current, at 24 volts,
was about the same as the current flow for the same test piece at 12 volts. Interesting.
Test Pieces:
-The steel handle of a thin walled acid brush heated up to medium orange in about 15 seconds.
-A 6D nail glowed red in about 30 seconds
-A 1/4 inch square piece of solid steel rod glowed red in about 45 to 60 seconds.
-1 A 1/2 inch square piece of solid steel rod glowed red in about 1 1/2 or 2 minutes.
-Right after those tests, I tried the piece of rusty half inch water pipe, which, as you know, is about 7/8" in actual outside diameter and about 1/2 inch inner
diameter.
It started to smoke in about 30 seconds and then at about 60 seconds, both Mosfets exploded and began to actually burn. Yes, two tiny fires for about
30 seconds. Of course the current flow dropped to zero as soon as the fireworks started.
I had been casually observing the ammeter during this time. Wish I had been looking more carefully, but I think the current went well over
20 amps.
That's why I say the you MUST have an ammeter!
Stay UNDER 20 amps!!!
5.2. How I am attempting fix them
First I had to relearn how to desolder stuff without damaging the board beyond repair.
One problem is that when the Mosfets go, it's usuall because of overheating and, in a couple of cases, this distorted the traces on the board.
I did find a message on the Banggood website that tells a user that it's any or all of the active components that go bad.
That's the Mosfets, the 12 volt one watt zener and the fast diode. (2 of each, per circuit board) So I ordered several of each.
As of November 24, 2016, I have removed all of those active components from 3 boards and I have tested them as best I could.
One problem has been the removal of all those parts. It is hard to get at the little screws that holds the Mosfets in place. I found that a tiny
straight blade screwdriver can be uses to get the screws loose. An alternative would be to remove the toroidal inductors to gain better access.>br>
But, if you can get the Mosfets and their heatsinks off, you will have plenty of room to work.
A good solder sucker and some fresh solder wick helps to get the joints clean.
What I found that has failed:
Not sure which goes first, the chicken or the egg, but the Mosfets sure can heat up and go "boom"! To make things worse,(and I can't believe they did this) there is
absolutely NO sign of heat sink compound on any of the 6 Mosfets that I have removed!!!
But, I actually found only 2 of those 6 Mosfets to be bad. Every one of my three bad boards had ONE bad zener diode.
The only other component that I can point to was that one lead on one of the 470 ohm resistors had actually broken and was making only intermittent contact with its
pad.
What made this a bad deal is that this was on a board that had previously failed. Not sure which one. I had decided to simply replace the Mosfets and nothing else.
A bad idea, looking back. Those 470 ohm 5 watt resistors are relatively heavy and they stand on end. I have ho idea how much vibration that board may have been
subject to on its long way from China. I don't know whether that bad resistor connection had caused the original failure or not.
But, when i powered up the repaired board, I saw a quick, large deflectio of the ammeter, and then nothing.
As I write this, I am just completing a complete active component replacement of my best chance board. I added wire to the Mosfet traces that had been compromised.
We will see how that one goes.